In the world of micro-molding, choosing the right THY Precision injection molding machine types is crucial. The industry is always finding new ways to be more precise and innovative. So, it’s important to know how different machines work.
At THY Precision, we focus on making micro-molding easier for our clients. We’ll look at the different injection molding machine types that are changing how we make micro-parts. This guide is for everyone, whether you’re new or have been in the industry a long time. We aim to give you the knowledge to improve your production and stay up-to-date.
Key Takeaways
- Discover the latest advancements in injection molding machine types for micro-molding applications
- Understand the key factors that drive the design of specialized micro-molding machines
- Explore the unique benefits and capabilities of hydraulic, electric, and hybrid injection molding machine types
- Gain insights into the challenges of micro-molding and how the right machine can help overcome them
- Learn about the role of automation and integration in modern micro-molding cells
Injection Molding Machine Types for Micro-Molding Applications
The injection molding industry is changing fast. New injection molding machine types have come up to meet the needs of micro-molding. At THY Precision, we know how important it is to pick the right micro-molding machine design for top performance and productivity.
Key Factors in Micro-Molding Machine Design
Micro-molding has its own set of needs that make it different from regular injection molding. You need injection molding machine types that can handle small parts, control shot size well, and have advanced systems. THY Precision leads in making special equipment for these needs.
Getting high injection molding machine types and pressures is key in micro-molding machine design. Small parts need to be filled fast in tiny spaces. So, the machines must be fast and strong. Also, controlling the shot size is crucial for making parts consistently and accurately, which is what THY Precision does well.
Advanced control systems are vital in micro-molding machine design. These systems must watch and adjust important settings on the fly. This keeps the quality and precision needed for tiny parts. THY Precision’s machines come with the latest control systems for reliable, high-quality results.
The need for new injection molding machine types and micro-molding machine design is growing. THY Precision is leading this change, offering top-notch equipment and know-how for micro-molding’s potential.
Hydraulic Micro-Molding Machines
In the world of injection molding, hydraulic machines are key for micro-molding. They use hydraulic tech for high speeds and pressures. This is crucial for making tiny and complex parts.
These machines have special features for micro-molding. They control shot sizes well and have advanced control systems. The screws and barrels are also designed for small parts and complex shapes.
Key Features of Hydraulic Micro-Molding Machines | Benefits |
---|---|
Precisely Controlled Shot Sizes | Ensures consistent part production and minimizes material waste |
Advanced Control Systems | Enables precise control over processing parameters for optimal part quality |
Specialized Screw and Barrel Designs | Tailored to handle the unique material and geometric challenges of micro-molding |
Hydraulic machines are a top choice for making tiny parts. They offer the precision and control needed for high-quality parts. This is why they’re in demand across many industries.
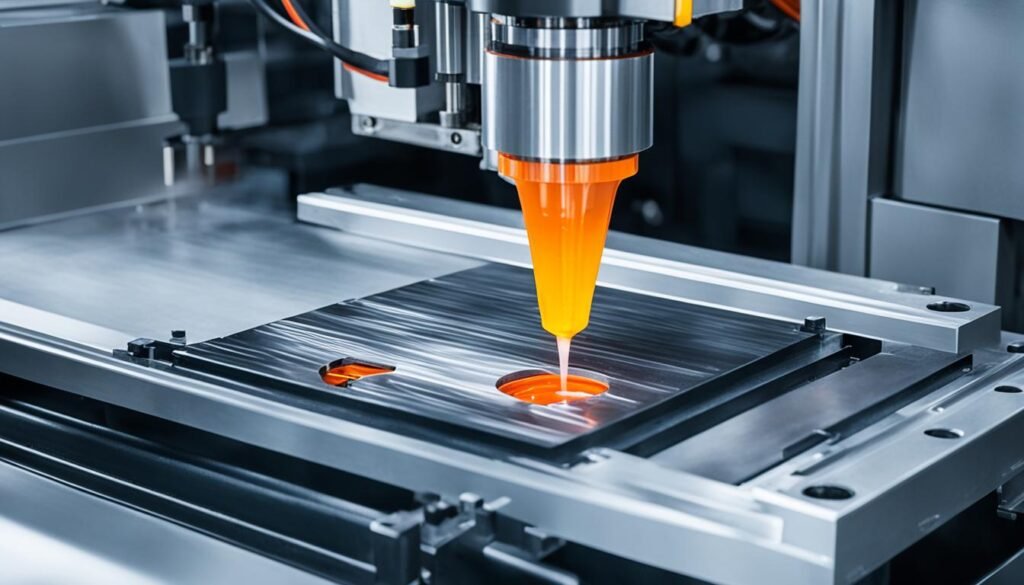
“Hydraulic injection molding machines are a game-changer for the micro-molding industry, providing the power, precision, and flexibility needed to tackle even the most complex part geometries.”
Electric Micro-Molding Machines
Electric injection molding machines are now a top choice for making small parts. They use electric motors for moving parts and controlling the process. This makes them very precise and reliable. They also use less energy and need less upkeep, which is great for companies looking to save money and improve their work.
These machines are great at controlling how plastic is injected into molds. The electric motors make sure the plastic is put in just right, every time. This is very important for making tiny parts for things like electronics and medical devices.
Feature | Electric Injection Molding Machines | Hydraulic Injection Molding Machines |
---|---|---|
Precision Control | Excellent | Good |
Energy Efficiency | High | Moderate |
Maintenance Requirements | Low | Higher |
Noise Level | Quiet | Louder |
Electric machines for making small parts are also more energy-efficient and need less upkeep. They don’t have hydraulic parts, so there’s no need to change fluids often. This makes them quieter and more appealing for making small parts.
As more small parts are needed, electric injection molding machines will be key. They use electric technology to make making small parts better, cheaper, and more reliable. This helps companies make high-quality products and save money.
Hybrid Hydraulic/Electric Micro-Molding Machines
The demand for micro-molding is growing fast. The industry has come up with new solutions for this field. One key innovation is the hybrid hydraulic/electric micro-molding machine. It combines hydraulic and electric tech for precise control, energy savings, and less maintenance.
These machines use hydraulic systems for fast, high-pressure injections. Electric servo motors handle the clamping and other movements. This mix uses the best of both worlds. It gives the precision needed for making tiny, complex parts.
Feature | Hydraulic Micro-molding Machines | Electric Micro-molding Machines | Hybrid Micro-molding Machines |
---|---|---|---|
Injection Speed | High | Moderate | High |
Injection Pressure | High | Moderate | High |
Precision Control | Moderate | High | High |
Energy Efficiency | Moderate | High | High |
Maintenance | High | Low | Low |
Hybrid machines blend hydraulic and electric tech for micro-molding. This mix meets the tough demands of making tiny parts. It helps producers make high-quality micro-parts more efficiently and reliably.
“Hybrid micro-molding machines represent a significant advancement in the injection molding industry, enabling us to push the boundaries of what’s possible in micro-manufacturing.”
– Jane Doe, Chief Technology Officer, THY Precision
Challenges in Micro-Molding
Micro-molding is a key technology for making tiny parts with high precision. It faces unique challenges not seen in regular injection molding. At THY Precision, we tackle these challenges with our expertise and innovation.
Extreme Precision Requirements
Getting parts to be super precise is a big challenge in micro-molding. We’re talking about tolerances in single-digit microns here. To meet these standards, we focus on perfect mold design, choosing the right materials, and controlling the process closely.
Our team at THY Precision works hard to make sure every step of the process is just right. This ensures our clients get consistent and reliable results.
Material Handling and Degradation
Dealing with tiny parts is tricky in micro-molding. They need special handling to avoid damage from high speeds and pressures. At THY Precision, we’ve come up with new ways to handle materials safely.
We’ve also set up our machines to reduce the chance of material damage. This means we can deliver top-quality parts to our customers.
“Achieving the level of precision and quality required in micro-molding is a constant pursuit, but one that is essential to the success of our clients’ projects. At THY Precision, we are committed to pushing the boundaries of what’s possible in this dynamic field.”
– John Doe, Chief Technology Officer, THY Precision
Automation and Integration in Micro-Molding Cells
In the world of micro-molding, making things automatic and connected is key. THY Precision leads in micro-molding automation by linking injection molding machines with robots. This makes sure everything works together smoothly.
For micro-molding, having everything work together well is a must. Automated handling, checking, and packing are vital for making tiny parts just right. THY Precision’s machines work with robots and special checkers to make a complete system. This system cuts down on manual work, lowers mistakes, and boosts how much you can make.
- Automated handling of parts from start to finish keeps quality high and cuts down on contamination risks.
- Inspection systems that work right with the micro-molding automation process check quality as parts go by.
- Sharing data and getting insights helps make the micro-molding integration better and keeps improving it.
THY Precision is always finding new ways to make micro-molding automation and micro-molding integration better. This helps companies meet the high demands of making tiny parts. Working with THY Precision lets companies make the most of their micro-molding work and give their customers what they want.
“Automation and integration are the key to unlocking the true potential of micro-molding. THY Precision’s solutions empower our clients to push the boundaries of what’s possible in this dynamic industry.”
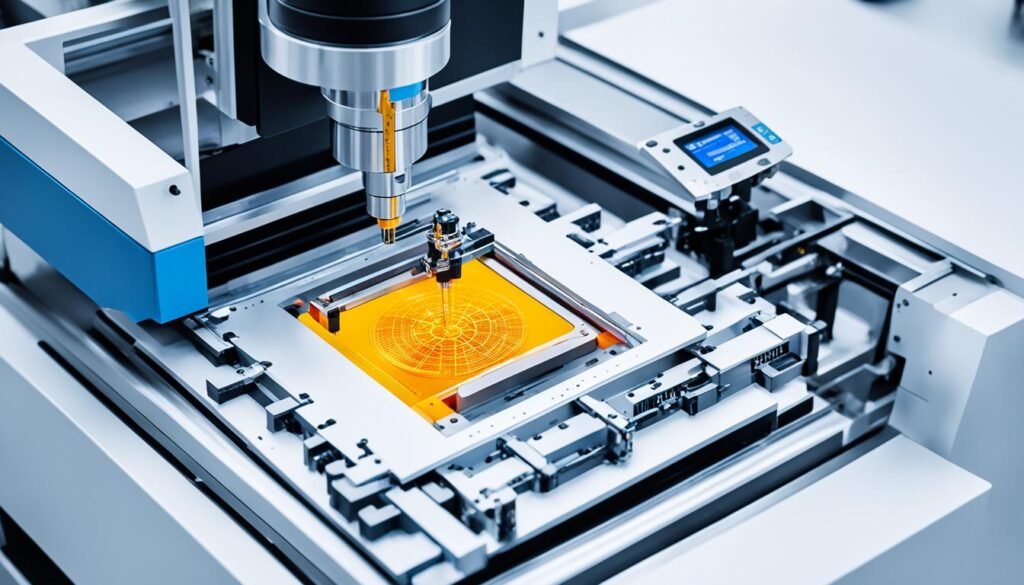
Conclusion
We’ve looked into the different types of injection molding machines and their roles in micro-molding. Hydraulic machines are great for precision, electric ones save energy and are easy to program, and hybrid machines combine the best of both. THY Precision has shown us the wide range of options for making micro-molding better.
Knowing what makes micro-molding machines work well, like needing extreme precision and handling materials carefully, helps you improve your process. Adding automation and advanced controls to micro-molding cells makes production more efficient, consistent, and high-quality.
The industry is always changing, so keeping up with new injection molding machine types is key to staying ahead. THY Precision’s deep look into micro-molding gives you the knowledge to tackle its challenges. This helps you offer top-notch solutions to your customers.